A Look Forward With Charlie Carter, President of AISC
We spoke with Charlie Carter, current president of the American Institute of Steel Construction, about challenges, opportunities and bright spots in the building and steel industries and what he foresees for both.
Barriers to Innovation and Potential Solutions
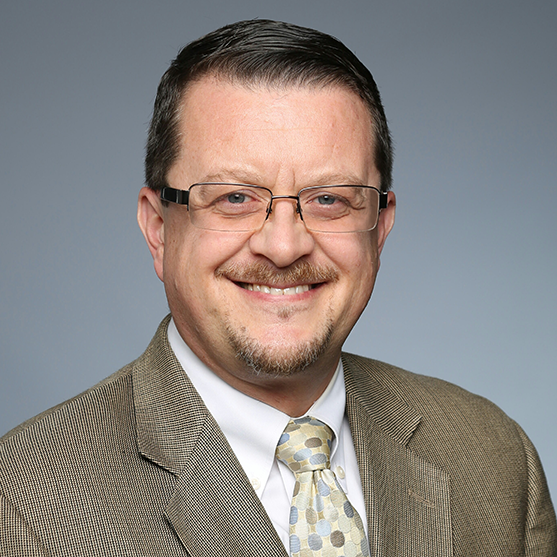
Charlie Carter has been president of the American Institute of Steel Construction (AISC) for the past six years, but he has held many technical roles at the organization over the last 32 years. When asked about barriers to innovation in the building industry, he cites divisiveness as a key blocker. “Some project team managers prefer to limit collaboration and may even prefer to keep the participants in adversarial positions. When something goes wrong, that gets even worse, and you can’t innovate if you can’t even collaborate.”
He also sees generalized resistance to change working against innovation, though he has seen positive shifts when all parties understand the benefits of adjusting how things are done. “That’s our biggest barrier as an industry — what is tends to be a practical restraint on what can be. Though the more people see what’s in it for them, the more likely it is we’ll be able to overcome that and innovate.”
The AISC has a clear role to play in moving the industry forward through setting standards, Charlie says, stressing that when they standardize guidelines or publish a document, it’s done with expert input and the goal of producing a solution that’s useful in the marketplace.
Innovation in Erection and Fabrication
When asked about the potential for innovation in erection and fabrication, Charlie sees the continuation of a 30-year trend toward automation that increases efficiency. “Thirty years ago, it was the beam line that was revolutionizing the shop, and a constant succession of similarly automated equipment has followed. Today, it’s the scanning and assembly robot that’s kicking off the modern shop revolution.”
Because these robots can do everything from scanning shapes and parts, locating them, accounting for tolerances and variations, tacking, and fillet welding, they are five times faster than traditional fabrication processes. Additionally, time efficiencies are achieved through the software they run, which outlines the precise work schedule, including downtime for routine system maintenance. All of this can make workers uneasy, and the initial cost is a hurdle, but Charlie says the benefits are clear. “Workers think robots will replace them. But what they learn is that they must run the robot, and the impact is not that the shop needs only 20% of the workers but rather that the shop can do five times more work and be more profitable as they do it.”
Charlie believes the next step for robots is moving them to the job site. “These robots are already moving their tools in three dimensions in the shop. We just need to figure out how to make them work from a base that climbs the steel and allows the steel erector to leverage that speed in field work.” He also sees the potential for robots to evolve to handle groove welds and even bolting, further increasing efficiency.
“Need for Speed” Progress and Industry Response
We asked Charlie for updates to the “Need for Speed” program that was created by former AISC board chair Jack Klimp. It originally aimed to reduce design and construction time by 50% by 2025 through efficiency boosters like SpeedCore and FastFloor. Charlie says the news is good. “The December 2022 issue of AISC’s Modern Steel Construction magazine highlighted dozens of companies with resources and products that are making steel design and construction faster for buildings and bridges. They already created the speed to meet our initial goal. We’re now working on the second 50% reduction.”
Charlie also reports that fabricator groups and erector groups have been very interested and excited about the initiative, citing the use of SpeedCore in the construction of Seattle’s Rainier Square Tower. “They thought it would trim four months off the construction schedule and save the owner $8 million. It actually saved almost 10 months and $22 million. And everyone leans in when I note that they were erecting the building at four floors a week after the learning curve. Even with the learning curve at the start, they were doing two floors a week. That’s incredible.”
On-Site Preassembly and Panelization
While panelization isn’t new, SpeedCore and FastFloor are shining a light on the time and cost benefits of preassembly for both commercial and residential projects. Charlie says, “It makes a lot of sense to me. Build everything you can in a shop or on the ground and then do the rest at height.”
One challenge is that some panelized approaches are connected to patents and proprietary products, so builders have concerns about recouping fees for using these kinds of products or technologies. However, Charlie notes that AISC has intentionally kept SpeedCore and FastFloor free to all in order to prompt adoption.
The Rise of Bolting and Screwing
We asked whetherfield welding on steel will eventually be eliminated and replaced by bolting and screwing, and Charlie sees room for both systems. “I see bolting and screwing and shot pins in some areas, and there’s tremendous interest in it in seismic areas for deck attachments because of higher ductility in the fastener. I think welding and the associated requirements will adapt to higher-strength steels too as their use becomes more prevalent. Bolts will adapt in the ways they need to as well.”
The Great ASD vs. LRFD Debate
In the ’90s, AISC attempted to replace ASD with LRFD by only including LRFD in specification updates, but most engineers continued using the outdated 9th edition ASD. AISC published the 13th edition with both ASD and LRFD treated equally, and most engineers have continued to use whichever method they were using before that time. On the plus side, they get to use a current and updated version of their chosen approach.
Charlie says survey results over the last 30 years have remained consistent, and any confusion is not an issue from the point of view of AISC due to the publication of the 2005 unified AISC Specification. He describes the current standard in unified format as, “The best of both, and it can be used in the format of your choosing. Some people still think there are differences, like ASD being linear and LRFD being nonlinear. But that’s incorrect.” He also emphasizes that ASD and LRFD give the same results. “LRFD and ASD are equivalent, and there are no differences in behavior or assumptions between them. The only difference is that we’re using a set of phi-factors as multipliers to reduce the nominal strength in LRFD versus dividing by omega-factors to reduce that same nominal strength for ASD. The equation is the same, and the behavior of the steel is the same.”
He also highlighted a known issue with ASCE 7 ASD load combinations having a different basis than ASCE 7 LRFD load combinations. He says, “Their LRFD load combinations better match what we understand today about loads and their combinations for design calculations, whereas their ASD load combinations are formulated differently. That can create differences in design entirely because of the differences in their load combinations. We’re working with ASCE 7 to address that.”
Steel Availability
As many are aware, the demand for steel in buildings and bridges remains very high. Charlie says this has spawned a spirit of partnership. “I see steel fabricators collaborating extensively to match their shop time and that of their collaborators to meet the demands of their projects. Mills and service centers are also helping to make that all work. The steel industry is meeting this very high demand, and availability seems to be managed about as well as anyone could expect.”
The Impacts of Steel Tariffs
The AISC provided input when Section 232 tariffs were first proposed, testifying at the Department of Commerce hearings with three recommendations:
- Consider applying a strong “Buy America” requirement as that policy already exists and is known to be successful.
- Make the “Buy America” requirement applicable to all critical infrastructure projects. That’s also a defined term, and it’s almost entirely applicable to projects that have taxpayer funding.
- If tariffs are implemented with or in place of the above, cover the HTS codes for fabricated products in addition to mill products. Otherwise, we fear you will actually be incentivizing importers of foreign material to begin fabricating those same foreign materials for import in order to evade the tariffs.
The tariff-only approach was selected and made applicable only to the HTS codes for mill material. Unfortunately, Charlie says AISC has seen the predicted impacts. “Imports of fabricated products are now about double where they were in 2018. It’s still a small percentage in the larger picture, but don’t you hate to be right on something like this?”
AISC Membership
AISC membership reflects the support of the industry and design sectors, with roughly 1,000 fabricators and 35,000 engineers. The wider membership community includes mills, HSS manufacturers, service centers, detailers, erectors, benders/rollers, allied industry people like product and equipment manufacturers, software vendors, architects, GCs and CMs, inspectors, code officials, professors, and students.
Charlie highlighted the increasing focus on the role of architects at AISC, acknowledging their role in the decision-making process and citing the architecture-driven experience on the floor of the steel conference in Charlotte in April. He says, “We’re going to develop that area at AISC. We’ve not done enough with it to date. We have a few staff members who are architects by education and practice, and they are helping us jump-start it. I foresee that we will find people in the architecture community who will be as influential for the future of steel as Ludwig Mies van der Rohe was in our past.”
While AISC is a domestic organization, they do engage worldwide with similar organizations, sharing research and information to benefit work around the world. Additionally, the International Steelwork Contractors Group was created to foster information sharing between English-speaking countries.
Industry Predictions
When asked what he foresees for the industry, Charlie says, “Well, you’re in luck because I do have a crystal ball. My Syrian great-grandmother used to use it when I was a kid and I have it now.”
Here’s what he predicts:
- Frictionless project collaboration methods will disrupt the current marketplace.
- Steel, which is almost entirely produced by electric arc furnace methods for structural products in the U.S., will become the first real zero-carbon structural material as the greening of the electric grid progresses far enough.
- Robots will continue to transform shops and job sites as well as how people work.
- Devices to eliminate problems we now solve structurally (like vibration) will be invented.
- Performance-based design will overtake prescriptive code-based design, leading to increased design creativity.
Ending on a Positive Note
Charlie sees a bright future for the steel industry, calling it “the industry of value.” He continues, “My friend John Cross, who retired from AISC a few years ago, was always keen to point out that steel solutions are the only ones that deliver well across all desirable attributes, and concrete, wood and masonry all have to make excuses as they focus on one or two attributes. Think about the six things that seem to matter the most in the marketplace today: cost, quality, speed, sustainability, resilience and adaptability. We are the only industry that can deliver value on all six simultaneously. We need to remember that and, more importantly, we all need to tell everyone we work with who makes decisions about choosing steel. We need to get our entire industry telling everyone. We are the people with the very best story to tell.”