Discussing the Present and Future of Fire Resistance Design With Steel Joists
Five experts weigh in on various aspects of fire resistance design and cover topics such as the difference between prescriptive and performance-based design, the impact of building codes, the potential future of fire design, and much more.
- Mark Webster, P.E., Senior Consulting Engineer, Simpson Gumpertz & Heger
- David Jacoby, Principal, Engineering Mechanics and Infrastructure Division Head, Fire Engineering, Simpson Gumpertz & Heger
- Joe Pote, P.E., Director of Research and Development, New Millennium
- Walt Schultz, Structural Research Engineer, Nucor
- Russ Balvin, Research and Development Engineer, Nucor
Prescriptive vs. Performance-Based Design
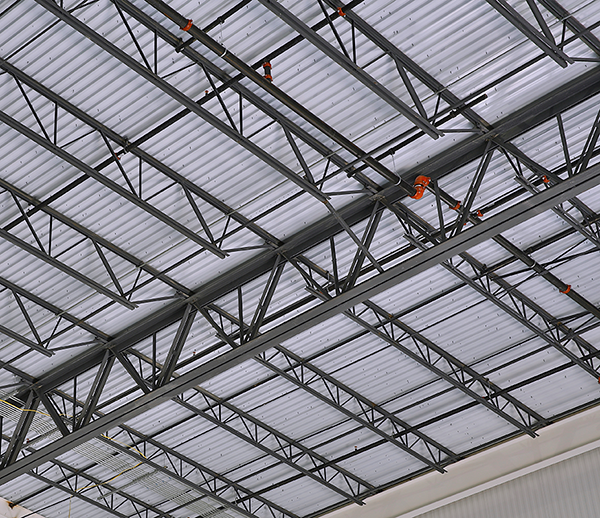
Two common design methods are available for fire resistance design: prescriptive and performance-based. Prescriptive design involves adopting preapproved assemblies that have demonstrated their ability to meet industry standard test criteria. Performance-based approaches use project-specific testing or analysis to demonstrate that the design assembly is capable of resisting realistic fire scenarios with acceptable performance.
One benefit of prescriptive design is that it’s easy to follow and structures designed using this approach will typically perform adequately so long as the assembly is followed and fires encountered are within assumed parameters. But there is a downside to this. Joe says, “Prescriptive design tends to work against anything innovative. If you’re trying to use a new approach or material, you can’t find an assembly that exactly matches. You’re stuck with having to do multiple fire tests because one is never enough.” If you can’t find a fire-rated assembly that works for your project, there are guides in the Underwriters Laboratories (UL) directory that allow substitutions. Otherwise, you’re looking at either a performance-based solution or getting something tested.
With a performance-based design approach, it’s easier to do something innovative, and you can see what’s actually there versus what’s used in a standard test. But this approach isn’t perfect either. David says, “The problem is time and the need to be knowledgeable of the systems and how they perform. You need to know the material properties of what’s being used — especially when you’re using new materials or in a new arrangement — to accurately model them.”
Russ adds, “The use of performance-based design does and can be greatly influenced by the knowledge of the authority having jurisdiction. If you’re in a situation where they really haven’t ever dealt with that before on any level, not just fire ratings, that can very much be an uphill battle today. In the next 20 years, we’re hoping that changes.”
Changes in Building Codes
Over the years, building codes have changed a lot regarding fire resistance, especially when it comes to aspects that affect structures. But the fundamentals of having a safe building have not changed, just the methodology of how to get there in your design.
David says, “In the last 20 years, and post-9/11, there were a bunch of changes that came into the building code specifically that addressed the fire rating of structures, like looking at spray-applied fireproofing materials (SFRM) and their adhesion and how to fireproof a bar joist type arrangement.” Fire life safety is done with redundancies and overlapping systems to address any multitude of issues that might come up over the life of a building, so the installation of safety measures such as sprinklers does not eliminate the need for these other fire prevention solutions.
Joe adds, “You have to look at everything and consider all your options and how things work together. Although the Early Suppression Fast Response Systems (ESFR) have eliminated the need for a lot of the other fire protection requirements in single-story structures, you have to look at the total building and what all you’re trying to do with it.”
Joist Fireproofing and Intumescent Paint
When it comes to steel joists that will receive SFRM, people often wonder if it should be manufactured with or without paint. As it turns out, most manufacturers can do it however the customer needs it. Walter says, “Basically it can be either way. It’s tested, and a lot of them with direct-applied fireproofing will say painted or unpainted. When you get to certain structural shapes, if you’re using it, then there’s a width limit on it. But basically, the fireproof protection encapsulates the joists, and when it’s tested, the paint breaks down, but the fireproofing is still there.”
Russ later adds, “And at our company it would be the same way. We would do our best to try to encourage them to leave the paint off because we just know the adherence is a little better, but if they want it painted, we’re going to give it to them.” Some manufacturers will need an application of a bonding agent before applying the SFRM.
Intumescent paint, a material that when heated expands and forms a charred layer that creates insulation to protect the structure underneath it, has been used for many years now. It’s a well-proven product, though it can be labor-intensive to apply compared to other products and therefore is expensive.
“In the United States, you’re really only seeing intumescent paint in areas where architecturally they want to see the structure for one reason or another,” says David. “Because of the cost associated with it, its application is relatively limited. Overseas, we’re starting to see intumescent paint being used more, where they’re assembling parts off-site and bringing them on-site. So doing intumescent paint in the factory means you have one less trade in theory out on-site while you’re doing assembly.” In Europe, many are doing it in the shop under controlled conditions which Russ mentions is ideal. But he also points out that it adds complications to much of the process, such as construction on-site and not being able to weld around intumescent paint.
Higher-Strength Steel Testing
About 15 years ago, some research was conducted that would promote the use of vanadium in the industry. Vanadium is a metallic element that when alloyed in steel, in trace quantities, can strengthen it without really changing the manufacturing process. Simpson Gumpertz & Heger initially looked at construction applications that could benefit from these properties and quickly settled on fire as being one that really needed to be addressed.
Mark explains further how they approached testing. He says, “There was nothing above 50 KSI in the UL directory. What was needed was to convince UL to allow higher-strength steel. Does every single assembly need to be tested again with the higher-strength steel? We started with one assembly and did a comparative test: two joists with 70 KSI steel and two with 50 KSI steel. And these joists needed to be loaded to their design strength. For performance, in terms of time to failure and deflections, the 70 KSI joists were just barely worse than the 50 KSI joists.” Because the joists didn’t meet the test criteria for deflection and strength, it wasn’t a direct substitution. An analytical study had to be done to say when using 70 KSI, you need to use members that will give a little more strength to ensure that it’ll meet the fire criteria.
Although the results were interesting, this has had minimal impact on the steel joist industry so far. Further research with SJI showed that the main deal breaker was the weld criteria because of more preheat requirements. Joe says, “There were a lot of discussions around having to make sure the steel was stored at higher temperatures or preheating it before bringing it onto the joist production line. Ultimately there were issues and SJI decided not to proceed, so there is no standard SJI joist that goes above 50 KSI. However, the testing is still valid — it is in UL and the insight gathered can be taken advantage of.”
Comparing Hot Rolled Steel to Cold Formed Steel
Recently, SJI conducted testing with UL comparing hot rolled steel to cold-formed steel. Mark says, “The results were very favorable with the cold-formed versus hot rolled. And there was no reason to expect that the cold-formed would perform any worse because the metallurgy of the steel is basically the same. It’s just a matter of the section geometry being different. And UL, I think it was concerned about the cold-formed steel, but based on the rules we agreed to, the cold-formed performed equal or better than the hot rolled specimens we tested.”
Joe adds, “It was a four-beam test. We had two joists constructed of hot-rolled materials and two joists constructed of cold-formed materials: cold-formed double angle top and bottom chord and cold-formed channel webs. The joists constructed of hot-rolled materials were merchant bar, double angle top and bottom cords, and single continuous crimp angles for the webs. Then the fireproofing was applied to where one of each was set up for a one-hour fire rating and one of each was set up for a two-and-a-half-hour fire rating. They were each loaded based on their theoretical capacities and tested under elevated temperatures, and the cold-formed performed better than the hot rolled.” The main hurdle getting in the way was coming up with an approach that UL was happy with according to the group.
The Future of Fire Resistance Design
Many speculate that we’ll be seeing more performance-based fire resistance design, and that design criteria incorporated into the building codes in the future. David says, “We certainly do see more performance-based design coming. On the structural side, in 10 to 20 years, we will probably be talking about different materials. It’s going to come with its own set of fire problems. I think we will see much more emphasis on the environment and sustainability, which will have impacts on fire life safety.”
Joe says that he believes the research he and Mark are doing with UL and trying to define a way of addressing the change in massivity between assemblies that have been tested with rods may impact fire design as well down the line. He hopes these new insights will help bring old assemblies from the last 20 years and allow them to be used again with some conversion equations.
Regarding what should be addressed in SJI’s Technical Digest 10 revisions based on new insights, many would like to see some of the new research being worked on included in the revisions. Joe says, “I would like to see the higher-strength steel results included. The cold-formed versus hot rolled — that’s actually well-defined as well — and should be part of the revised TD 10. There are a few remaining questions on the massivity of joist members that we would like to resolve before we publish that updated Technical Digest and get that included.” Walter added, “In addition to what Joe said, just update the directory. Some designs fall out, and some are revised and added to.” With more research and testing to be done and published, it looks like fire resistance design and its impact on building codes will continue to evolve in the coming years.